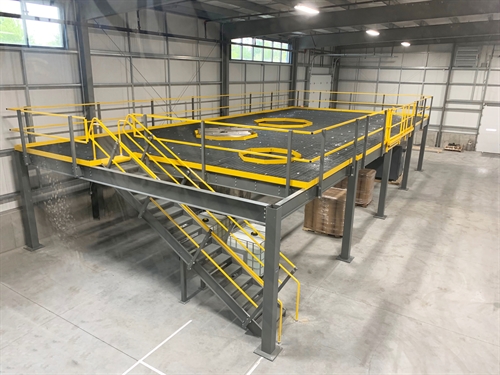
The Challenge
By their very nature, cosmetic and beauty products are comprised of ingredients that are highly biodegradable. If left unchecked, unwanted microbiological growth can break down these products, making them unpleasant and unsafe for consumer use. To prevent this from happening, antimicrobials are added to the product during the manufacturing process to inhibit the growth of contaminants. These are sourced from a reputable manufacturer.
One of the nation’s premier manufacturers of conventional, naturally derived and alternative multifunctional antimicrobials and preservatives is located in Lincoln, Rhode Island. As part of the company’s manufacturing process, a variety of different ingredients are added to tanks that are located inside a warehouse. While carefully assessing their production processes, it was determined that a safer, more efficient method for adding ingredients to the tanks was needed.
Wildeck’s Solution
After a careful consideration of all their available options, the manufacturing company decided to contact Bode Equipment Company, a trusted dealer of Wildeck’s material handling solutions. After surveying the facility where the antimicrobials and preservatives were produced and carefully considering all the project’s constraints, Bode Equipment Company knew that a custom Wildeck mezzanine was the right solution for the project.
Wildeck mezzanines are installed between the floor and the ceiling in an industrial setting to help a company make use of a building’s existing overhead space. In addition to increasing a building’s total square footage, a Wildeck mezzanine provides a sturdy and secure working level for the performance of critical manufacturing tasks.
Through a collaboration with Wildeck’s team of experienced structural engineers, Bode Equipment Company was able to present the manufacturer with a custom mezzanine design that measured 56’ by 26’. Three portholes through the mezzanine’s deck provided personnel with 360° access to the tops of the tanks, increasing the safety and efficiency with which ingredients could be added. Additionally, a deck height of 9’ 5” meant that the space beneath the mezzanine could be used for storage and personnel would be able to easily access the lower portions of the tanks for maintenance and operational tasks. Square tube handrail (painted safety yellow) was installed around the perimeter of the platform’s deck for added protection on the elevated work area. A sliding gate was also installed to provide a way for palletized materials to be safely transported to and from the top of the mezzanine via forklift.
“Given the customer’s unique needs, we knew that a team of creative and experienced structural engineers was needed, and our immediate thought was Wildeck,” said Scott Rose, Sr. Sales and Project Manager at Bode Equipment Company. “Wildeck’s mezzanine engineering capabilities are unparalleled by any other manufacturer in the industry.” Wildeck, Inc. is the largest U.S. manufacturer of industrial work platforms (mezzanines), vertical reciprocating conveyors (VRCs), rideable material lifts (RMLs), custom ladders, access platforms, and safety guarding products. In warehouses, distribution centers, manufacturing, logistics, and other operations, Wildeck products provide safe and efficient storing, lifting, and guarding solutions that can enhance your bottom line. Wildeck’s modern manufacturing facility and full-time staff of structural, mechanical and electrical engineers provide innovative, cost-effective, and performance-proven products that meet all applicable codes and industry safety requirements.
Wildeck, Inc. is a subsidiary of Holden Industries, a 100% employee-owned company. Please contact Dave Milner, Vice President Sales and Marketing at 262-549-4000, ext. 2030, dmilner@wildeck.com for more information on the complete line of Wildeck® products and services; or visit www.wildeck.com or